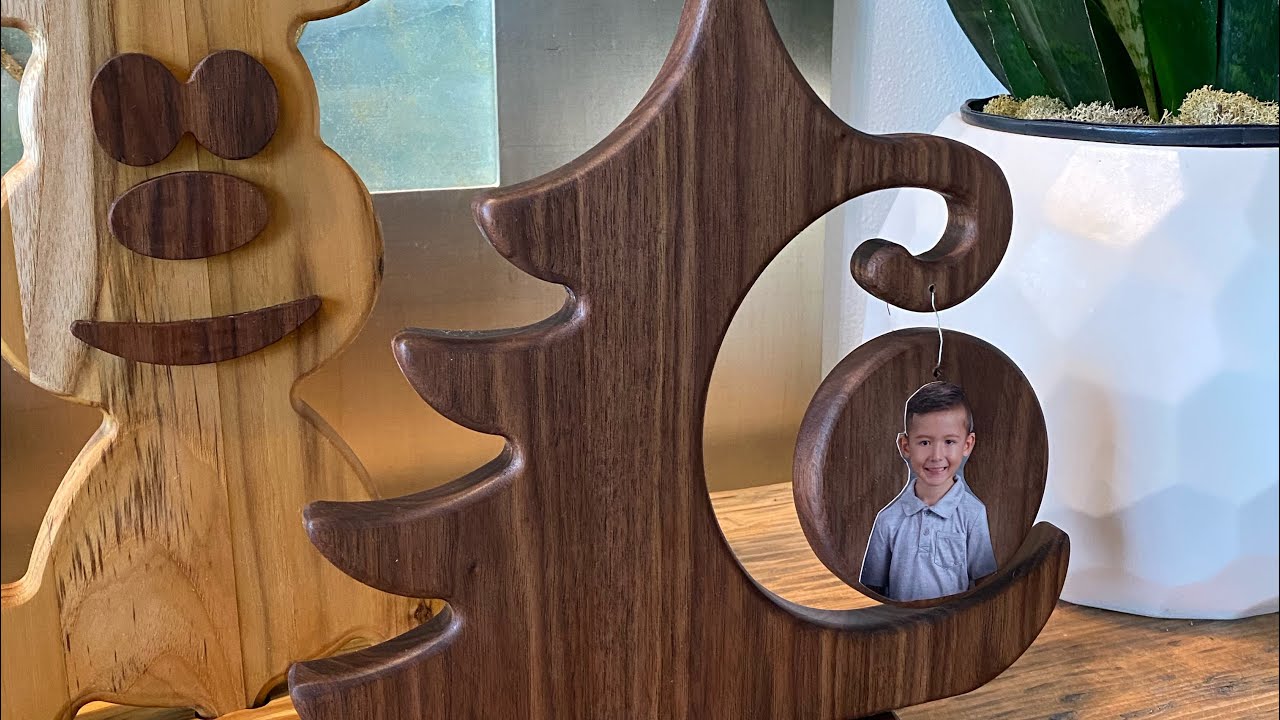
Profitable Cutting Board Projects to Sell This Holiday Season Hey there, crafty friends! The holiday season is just around the corner, and that means it's time to get those creative juices flowing. What better way to show your loved ones you care than with a handcrafted gift? And what better gift...
November 20, 2024